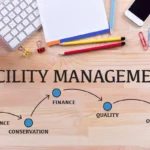
Communication: Building a Strong Relationship with Your Facility Cleaning Service
May 8, 2024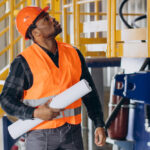
Leveraging Technology for Remote Facility Management and Monitoring
May 13, 2024Introduction
In the realm of facility management, preventive maintenance stands as a cornerstone of operational efficiency and cost-effectiveness. It is the proactive approach to maintenance, aiming to identify and rectify potential issues before they escalate into costly problems. This article delves into the significance of preventive maintenance in facility management, exploring its benefits, strategies, and implementation.
Understanding Preventive Maintenance
Preventive maintenance involves the regular inspection, upkeep, and repair of equipment, systems, and infrastructure within a facility. Unlike reactive maintenance, which addresses problems after they occur, preventive maintenance seeks to prevent breakdowns and prolong the lifespan of assets. It encompasses various tasks, from routine inspections and cleaning to lubrication, calibration, and component replacements.
Benefits of Preventive Maintenance
- Cost Savings
- By addressing issues proactively, preventive maintenance helps avoid costly repairs and replacements. Regular upkeep minimizes the likelihood of unexpected breakdowns, reducing downtime and associated expenses.
- Increased Equipment Lifespan
- Regular maintenance prevents premature wear and tear, extending the lifespan of equipment and facilities. Proper care and attention prolong the operational efficiency of assets, maximizing their return on investment.
- Enhanced Safety and Compliance
- Regular inspections and maintenance contribute to a safer working environment by identifying and rectifying potential hazards. Compliance with regulatory standards and industry guidelines is easier to maintain through consistent upkeep.
- Improved Energy Efficiency
- Well-maintained equipment operates more efficiently, consuming less energy and lowering utility costs. Regular servicing ensures that systems function optimally, reducing energy waste and environmental impact.
- Minimized Disruption
- Planned maintenance activities can be scheduled during off-peak hours to minimize disruption to operations. By addressing issues before they escalate, preventive maintenance helps maintain business continuity.
Strategies for Implementing Preventive Maintenance
- Asset Inventory and Prioritization
- Conduct a comprehensive inventory of all assets within the facility, categorizing them based on criticality and maintenance requirements. Prioritize maintenance activities based on factors such as asset importance, usage frequency, and potential impact on operations.
- Establishing Maintenance Schedules
- Develop maintenance schedules outlining the frequency and scope of preventive maintenance tasks for each asset or system. Consider factors such as manufacturer recommendations, historical performance data, and industry best practices when determining maintenance intervals.
- Utilizing Technology and Data
- Leverage technology solutions such as computerized maintenance management systems (CMMS) to streamline maintenance operations. CMMS software enables efficient work order management, asset tracking, and performance monitoring, facilitating data-driven decision-making.
- Training and Skill Development
- Ensure that maintenance personnel are adequately trained and equipped to perform preventive maintenance tasks effectively. Provide ongoing training and skill development opportunities to keep staff abreast of new technologies and best practices.
- Performance Monitoring and Continuous Improvement
- Implement performance metrics and key performance indicators (KPIs) to track the effectiveness of preventive maintenance activities. Analyze data to identify trends, areas for improvement, and opportunities to optimize maintenance processes continually.
Challenges and Considerations
- Resource Allocation
- Adequate resources, including personnel, time, and budget, are essential for implementing an effective preventive maintenance program. Balancing competing priorities and allocating resources efficiently is crucial for maximizing the program’s impact.
- Changing Technology and Requirements
- Advances in technology and evolving regulatory requirements may necessitate adjustments to preventive maintenance strategies. Facilities must stay informed about industry developments and adapt their maintenance practices accordingly to remain effective.
- Compliance and Documentation
- Maintaining compliance with regulatory standards and documentation requirements is critical for facility management. Establish robust record-keeping processes to document maintenance activities, inspections, and compliance efforts.
- Integration with Overall Facility Management Strategy
- Preventive maintenance should align with the broader facility management strategy and organizational goals. Integration with other operational processes, such as asset management, procurement, and risk management, ensures a holistic approach to facility maintenance.
Conclusion
Preventive maintenance is a fundamental aspect of effective facility management, offering a myriad of benefits ranging from cost savings to improved safety and operational efficiency. By adopting a proactive approach to maintenance and implementing strategies tailored to their specific needs, facilities can optimize asset performance, minimize downtime, and enhance overall productivity. Embracing preventive maintenance as a core principle empowers organizations to maximize the value of their assets and create sustainable, resilient facilities for the future.