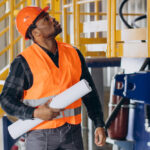
How to Develop a Facility Management Reporting System
June 21, 2024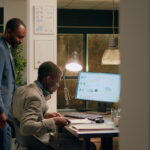
The Role of Facility Management in Operational Efficiency
July 3, 2024Facility management is a complex field that requires a blend of organizational skills, technical knowledge, and people management. Ensuring that a facility operates smoothly, efficiently, and safely is a challenging task. One way to meet this challenge is by implementing a robust quality control program. This article will guide you through the steps to develop and implement an effective facility management quality control program.
Understanding Facility Management Quality Control
Before diving into the implementation process, it’s crucial to understand what facility management quality control entails. Quality control in facility management involves setting standards for various aspects of facility operations, monitoring performance against those standards, and making necessary adjustments to improve efficiency and effectiveness. This encompasses everything from maintenance and cleaning to energy management and safety protocols.
Setting the Foundation: Assessing Current Practices
The first step in implementing a quality control program is to assess your current practices. This involves a thorough review of all existing procedures, policies, and performance metrics. Here are some steps to guide you through this assessment:
1. Conduct a Comprehensive Audit
Begin with a comprehensive audit of your facility’s current management practices. This includes evaluating maintenance schedules, cleaning protocols, safety measures, and other operational procedures. Identify areas where performance is lacking or where there are inconsistencies.
2. Gather Input from Stakeholders
Engage with various stakeholders, including facility staff, management, and occupants. Gather feedback on current practices and areas where they see room for improvement. This will provide valuable insights and help in identifying key areas to focus on.
3. Analyze Performance Data
Review historical performance data to identify trends and recurring issues. This can include data on equipment downtime, maintenance costs, energy usage, and safety incidents. Analyzing this data will help pinpoint areas that need improvement.
Defining Quality Standards
Once you have a clear understanding of your current practices, the next step is to define quality standards for your facility management program. These standards will serve as benchmarks against which you can measure performance.
1. Establish Clear Objectives
Set clear, measurable objectives for your quality control program. These objectives should align with your organization’s overall goals and should cover all aspects of facility management, including maintenance, cleanliness, safety, and energy efficiency.
2. Develop Standard Operating Procedures (SOPs)
Create detailed Standard Operating Procedures (SOPs) for all key processes. SOPs should outline step-by-step instructions for performing tasks, including maintenance routines, cleaning procedures, and safety checks. Ensure that these procedures are practical and easy to follow.
3. Set Performance Metrics
Define specific performance metrics to measure the effectiveness of your quality control program. These metrics can include response times for maintenance requests, frequency of cleaning activities, energy consumption levels, and the number of safety incidents. Establishing these metrics will allow you to track progress and identify areas for improvement.
Implementing the Quality Control Program
With your quality standards defined, it’s time to implement the quality control program. This involves rolling out new procedures, training staff, and establishing monitoring and reporting systems.
1. Communicate the Plan
Clearly communicate the quality control plan to all relevant stakeholders. This includes facility staff, management, and occupants. Explain the objectives, procedures, and performance metrics, and emphasize the importance of their role in achieving these goals.
2. Train Staff
Provide comprehensive training to all facility staff on the new procedures and standards. Ensure that they understand the importance of adhering to these standards and how their performance will be measured. Training should be ongoing to address any changes or updates to procedures.
3. Implement Monitoring Systems
Establish systems to monitor performance against the defined standards. This can include regular inspections, audits, and performance reviews. Utilize technology where possible, such as maintenance management software, to streamline monitoring and reporting processes.
Continuous Improvement: Reviewing and Adjusting
A quality control program is not a one-time implementation but an ongoing process of continuous improvement. Regularly review performance data, gather feedback, and make necessary adjustments to ensure the program remains effective.
1. Conduct Regular Reviews
Schedule regular reviews of the quality control program to assess its effectiveness. This can be done quarterly or annually, depending on the size and complexity of your facility. Use these reviews to identify areas where improvements are needed.
2. Gather Feedback
Continue to gather feedback from staff, management, and occupants. Their input can provide valuable insights into the effectiveness of the quality control program and highlight areas for improvement.
3. Make Adjustments
Based on the review and feedback, make necessary adjustments to the quality control program. This can include updating procedures, revising performance metrics, and implementing new technologies. The goal is to continuously improve and adapt to changing needs.
Leveraging Technology for Quality Control
Technology can play a significant role in enhancing the effectiveness of your quality control program. Here are some ways to leverage technology in facility management:
1. Maintenance Management Software
Utilize maintenance management software to streamline maintenance tasks, schedule preventive maintenance, and track work orders. This software can provide real-time data on equipment performance and maintenance activities, helping you to identify issues and make informed decisions.
2. Energy Management Systems
Implement energy management systems to monitor and control energy usage in your facility. These systems can provide insights into energy consumption patterns and help identify opportunities for energy savings.
3. IoT and Sensors
Integrate IoT devices and sensors to monitor various aspects of facility operations, such as temperature, humidity, and occupancy levels. These sensors can provide real-time data and alerts, enabling proactive maintenance and improving efficiency.
Case Study: Implementing a Quality Control Program
To illustrate the implementation of a quality control program, let’s look at a case study of a large corporate office building.
The Challenge
The facility management team at a large corporate office building was facing several challenges, including frequent equipment breakdowns, inconsistent cleaning standards, and rising energy costs. They decided to implement a quality control program to address these issues.
The Approach
- Assessment: The team conducted a comprehensive audit of current practices, gathered feedback from staff and occupants, and analyzed performance data. They identified key areas for improvement, including preventive maintenance, cleaning procedures, and energy management.
- Defining Standards: They established clear objectives for the quality control program, developed detailed SOPs for maintenance and cleaning tasks, and set performance metrics, such as reducing equipment downtime by 20%, achieving a 95% satisfaction rate for cleanliness, and cutting energy costs by 15%.
- Implementation: The team communicated the plan to all stakeholders, provided training to staff, and implemented monitoring systems using maintenance management software and energy management systems.
- Continuous Improvement: Regular reviews were conducted to assess the effectiveness of the program. Feedback was gathered from staff and occupants, and necessary adjustments were made to procedures and performance metrics.
The Results
Within a year, the facility management team achieved significant improvements. Equipment downtime was reduced by 25%, the satisfaction rate for cleanliness increased to 97%, and energy costs were cut by 18%. The quality control program not only improved operational efficiency but also enhanced the overall occupant experience.
Conclusion
Implementing a facility management quality control program is a comprehensive process that requires careful planning, execution, and continuous improvement. By assessing current practices, defining clear quality standards, implementing monitoring systems, and leveraging technology, you can enhance the efficiency and effectiveness of your facility operations. Remember, the key to a successful quality control program is ongoing commitment and adaptability to changing needs. With the right approach, you can create a safe, efficient, and pleasant environment for all occupants.