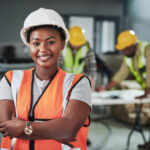
How to Implement Facility Management Best Practices
July 7, 2024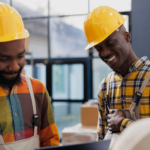
How to Develop a Facility Management Sustainability Plan
July 12, 2024Facility management is a multifaceted discipline encompassing various tasks and responsibilities, ranging from ensuring the smooth operation of building systems to maintaining a safe and productive environment for occupants. One of the most critical aspects of facility management is maintenance. Traditionally, maintenance has been approached reactively or preventively. However, the rise of technology and data analytics has introduced a more advanced approach known as predictive maintenance. This article delves into the importance of predictive maintenance in facility management, exploring its benefits, implementation strategies, and the future outlook.
Understanding Predictive Maintenance
Predictive maintenance is a proactive maintenance strategy that relies on data analysis, sensor technologies, and machine learning algorithms to predict when equipment and systems might fail. Unlike preventive maintenance, which follows a scheduled routine, predictive maintenance bases its actions on the actual condition of the equipment.
How Predictive Maintenance Works
Predictive maintenance uses various technologies such as:
- Sensors: These are installed on equipment to monitor variables like temperature, vibration, and pressure.
- Data Analytics: The data collected by sensors is analyzed to identify patterns and anomalies.
- Machine Learning Algorithms: These algorithms predict potential failures by learning from historical data and identifying signs of wear and tear.
The Benefits of Predictive Maintenance
The shift from traditional maintenance methods to predictive maintenance offers numerous advantages. Below are some of the most significant benefits.
Cost Efficiency
Predictive maintenance can lead to significant cost savings by reducing the frequency of unnecessary maintenance tasks and preventing costly downtime. By addressing issues before they escalate into major problems, facilities can avoid expensive repairs and replacements.
Increased Equipment Lifespan
Regular monitoring and timely interventions help in extending the lifespan of equipment. Predictive maintenance ensures that machines operate within their optimal parameters, reducing wear and tear and enhancing their overall durability.
Enhanced Safety
Predictive maintenance contributes to a safer working environment. By detecting potential failures early, it mitigates the risk of accidents caused by equipment malfunctions, ensuring the well-being of employees and occupants.
Reduced Downtime
Unplanned downtime can be costly and disruptive. Predictive maintenance minimizes downtime by addressing issues before they lead to breakdowns. This ensures that operations continue smoothly and efficiently.
Improved Efficiency
Facilities can optimize their operations by maintaining equipment at peak performance levels. Predictive maintenance helps in identifying inefficiencies and rectifying them, leading to enhanced productivity.
Implementing Predictive Maintenance
The transition to predictive maintenance requires careful planning and execution. Here are the key steps involved in implementing predictive maintenance in facility management.
Assessment and Planning
The first step is to assess the current maintenance strategy and identify the equipment and systems that would benefit most from predictive maintenance. This involves evaluating the criticality of each asset, the cost implications of failures, and the availability of data for analysis.
Integration of Technology
Implementing predictive maintenance necessitates the integration of various technologies, including sensors, IoT devices, and data analytics platforms. This requires collaboration with technology providers to ensure the seamless integration of hardware and software.
Data Collection and Analysis
Once the technology is in place, the next step is to start collecting data. This data must be continuously monitored and analyzed to identify patterns and predict potential failures. Facilities may need to invest in data analytics tools and hire data scientists or train existing staff to interpret the data effectively.
Training and Development
Employees need to be trained on the new maintenance protocols and the use of new technologies. This includes understanding how to interpret data, recognizing signs of potential failures, and taking appropriate actions based on predictive insights.
Continuous Improvement
Predictive maintenance is not a one-time implementation but a continuous process. Facilities must regularly review and refine their predictive maintenance strategies, incorporating new data and technologies to improve accuracy and effectiveness.
Case Studies: Success Stories in Predictive Maintenance
Real-world examples highlight the tangible benefits of predictive maintenance. Here are a few case studies demonstrating its impact.
Case Study 1: Manufacturing Plant
A large manufacturing plant implemented predictive maintenance on its critical machinery. By using vibration sensors and data analytics, the plant identified a pattern of increasing vibration levels in one of its key machines. Early intervention prevented a catastrophic failure, saving the company millions in repair costs and avoiding several weeks of downtime.
Case Study 2: Commercial Building
A commercial building utilized predictive maintenance to monitor its HVAC systems. The predictive analytics identified inefficiencies and impending failures, allowing the facility manager to schedule maintenance at convenient times. This not only improved the comfort of the building’s occupants but also reduced energy costs significantly.
Case Study 3: Data Center
A data center integrated predictive maintenance to ensure the reliability of its servers and cooling systems. By monitoring temperature and humidity levels, the facility management team could predict and prevent potential overheating issues, ensuring uninterrupted service and protecting valuable data.
Challenges in Implementing Predictive Maintenance
While predictive maintenance offers numerous benefits, it is not without challenges. Understanding these challenges can help facilities better prepare for implementation.
High Initial Investment
The initial cost of implementing predictive maintenance can be high, including the purchase of sensors, data analytics software, and the necessary infrastructure. However, the long-term savings and benefits often outweigh these initial costs.
Data Management
Collecting and analyzing large volumes of data can be daunting. Facilities need robust data management systems and skilled personnel to handle and interpret the data effectively.
Integration with Existing Systems
Integrating predictive maintenance technologies with existing systems can be complex. It requires careful planning and collaboration with technology providers to ensure compatibility and seamless operation.
Resistance to Change
Employees may resist the transition to predictive maintenance due to unfamiliarity with new technologies or fear of job displacement. Effective training and clear communication about the benefits of predictive maintenance can help overcome this resistance.
The Future of Predictive Maintenance in Facility Management
The future of predictive maintenance is promising, driven by advancements in technology and data analytics. Here are some trends and developments to watch.
Artificial Intelligence and Machine Learning
The integration of AI and machine learning is set to enhance predictive maintenance further. These technologies can improve the accuracy of predictions, identify more complex patterns, and offer automated insights, making maintenance processes more efficient and reliable.
Internet of Things (IoT)
The proliferation of IoT devices is expanding the possibilities for predictive maintenance. With more connected devices, facilities can gather richer data, leading to more comprehensive and accurate maintenance strategies.
Cloud Computing
Cloud computing offers scalable and flexible solutions for data storage and analysis. It enables facilities to handle large volumes of data and perform complex analytics without the need for extensive on-premises infrastructure.
Augmented Reality (AR)
AR can revolutionize predictive maintenance by providing real-time, interactive maintenance instructions and visualizations. Technicians can use AR to identify issues, understand complex systems, and perform maintenance tasks more effectively.
Conclusion
Predictive maintenance represents a significant advancement in facility management, offering a proactive approach to maintaining equipment and systems. By leveraging data and technology, facilities can achieve cost efficiency, increased equipment lifespan, enhanced safety, reduced downtime, and improved efficiency. While the implementation of predictive maintenance comes with challenges, the long-term benefits make it a worthwhile investment. As technology continues to evolve, predictive maintenance will become an even more integral part of facility management, driving innovation and efficiency in the industry.
In summary, the importance of predictive maintenance in facility management cannot be overstated. It is a powerful tool that not only improves the reliability and performance of equipment but also contributes to the overall success and sustainability of facilities. By embracing predictive maintenance, facility managers can ensure a safer, more efficient, and cost-effective operation, paving the way for a brighter future in facility management.