Ensuring Workplace Safety During Facility Cleaning
July 29, 2024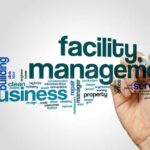
How to Conduct a Facility Management Gap Analysis
August 14, 2024Facility risk assessment is a critical process for identifying and managing potential hazards in any organization. Properly executed, it ensures the safety of employees, protects assets, and maintains compliance with regulatory requirements. This comprehensive guide will walk you through the steps of conducting a facility risk assessment, providing valuable insights and practical tips along the way.
Introduction to Facility Risk Assessment
Facility risk assessment involves a systematic approach to identifying, evaluating, and mitigating risks within a workplace or facility. These risks can range from physical hazards, such as machinery and structural integrity, to environmental and occupational health risks. The primary goal is to create a safer working environment and minimize the potential for accidents and injuries.
Why Conduct a Risk Assessment?
Conducting a risk assessment is not just a regulatory requirement; it’s a proactive measure that can save lives, reduce costs associated with workplace injuries, and enhance overall operational efficiency. By identifying potential hazards before they cause harm, organizations can implement appropriate control measures, thereby creating a safer and more productive environment.
Legal and Regulatory Requirements
Various laws and regulations mandate risk assessments, depending on the industry and location. Familiarize yourself with the relevant guidelines to ensure compliance. In the United States, the Occupational Safety and Health Administration (OSHA) provides comprehensive regulations for workplace safety. Similar regulatory bodies exist worldwide, such as the Health and Safety Executive (HSE) in the UK.
Step-by-Step Guide to Conducting a Facility Risk Assessment
Step 1: Identify the Scope and Objectives
The first step in conducting a risk assessment is to define the scope and objectives clearly. Determine the areas of the facility to be assessed and the specific risks to be identified. Objectives may include reducing workplace accidents, ensuring regulatory compliance, or improving overall safety culture.
Step 2: Assemble a Risk Assessment Team
Assembling a diverse team with varying expertise is crucial for a thorough risk assessment. The team should include personnel from different departments, such as safety officers, maintenance staff, operations managers, and employees who are familiar with the daily operations of the facility. Each member brings unique insights into potential hazards.
Step 3: Gather Relevant Data
Collecting relevant data is essential for an accurate risk assessment. This includes:
- Historical Incident Reports: Review past accident and incident reports to identify recurring issues.
- Inspection Records: Examine previous inspection reports for any noted deficiencies.
- Safety Data Sheets (SDS): Gather information on hazardous substances used within the facility.
- Equipment Manuals: Review operating manuals for machinery and equipment to understand potential hazards.
- Employee Feedback: Engage with employees to gather their observations and concerns about workplace safety.
Step 4: Conduct a Walkthrough Survey
A physical walkthrough of the facility is crucial for identifying hazards that might not be evident from documentation alone. During the survey, take note of:
- Physical Hazards: Uneven flooring, poor lighting, obstructed pathways, etc.
- Chemical Hazards: Storage and handling of hazardous materials.
- Biological Hazards: Potential exposure to harmful biological agents.
- Ergonomic Hazards: Workstations and tasks that could cause musculoskeletal injuries.
- Environmental Hazards: Noise levels, temperature extremes, ventilation issues.
Step 5: Identify Potential Hazards
Once the data is gathered, the next step is to identify potential hazards. These can be categorized as follows:
- Physical Hazards: Slips, trips, falls, machinery operation, electrical hazards.
- Chemical Hazards: Exposure to harmful chemicals, improper storage of hazardous substances.
- Biological Hazards: Exposure to bacteria, viruses, or other biological agents.
- Ergonomic Hazards: Repetitive strain injuries, improper lifting techniques.
- Environmental Hazards: Poor air quality, extreme temperatures, noise pollution.
Step 6: Evaluate Risks
Evaluating risks involves assessing the likelihood of an incident occurring and the potential severity of its consequences. This can be done using a risk matrix, which helps prioritize risks based on their impact and likelihood. The risk matrix typically has the following components:
- Likelihood: The probability of the hazard occurring (e.g., rare, unlikely, possible, likely, almost certain).
- Impact: The severity of the consequences if the hazard occurs (e.g., negligible, minor, moderate, major, catastrophic).
Step 7: Determine Control Measures
After evaluating the risks, determine appropriate control measures to mitigate them. Control measures can be categorized using the hierarchy of controls, which prioritizes methods based on their effectiveness:
- Elimination: Completely remove the hazard from the workplace.
- Substitution: Replace the hazard with a less dangerous option.
- Engineering Controls: Isolate people from the hazard (e.g., machine guards, ventilation systems).
- Administrative Controls: Change the way people work (e.g., training, signage, procedures).
- Personal Protective Equipment (PPE): Provide protective gear to reduce exposure to hazards.
Step 8: Implement Control Measures
Implementing control measures involves putting the planned interventions into practice. This may require:
- Training and Education: Ensure employees understand the risks and know how to use control measures properly.
- Procedural Changes: Update workplace procedures to reflect new safety protocols.
- Equipment Modifications: Install or modify equipment to reduce hazards.
- Monitoring and Maintenance: Regularly inspect and maintain control measures to ensure their effectiveness.
Step 9: Document the Assessment
Documentation is a crucial part of the risk assessment process. Record all findings, control measures, and actions taken in a comprehensive risk assessment report. This report should include:
- Scope and Objectives: Outline the purpose and extent of the assessment.
- Methodology: Describe the methods used to identify and evaluate risks.
- Findings: Detail the identified hazards and associated risks.
- Control Measures: List the control measures implemented and their effectiveness.
- Action Plan: Provide a timeline for implementing and reviewing control measures.
Step 10: Review and Update Regularly
Risk assessment is not a one-time task but an ongoing process. Regularly review and update the assessment to account for changes in the workplace, such as new equipment, processes, or regulations. Periodic reviews ensure that the risk management strategies remain effective and relevant.
Conclusion
Conducting a facility risk assessment is a vital part of maintaining a safe and compliant workplace. By following the steps outlined in this guide, organizations can systematically identify, evaluate, and mitigate risks, creating a safer environment for employees and protecting valuable assets. Remember, a thorough risk assessment not only fulfills legal requirements but also demonstrates a commitment to the well-being of everyone in the workplace.