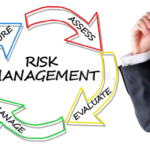
How to Conduct a Facility Risk Assessment
July 31, 2024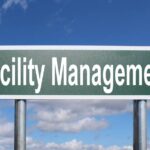
The Role of Facility Management in Community Engagement
August 16, 2024Facility management is a crucial aspect of maintaining any organization’s physical assets, ensuring that buildings, equipment, and systems are functional, safe, and efficient. However, over time, discrepancies can emerge between the current state of facility management and the ideal level of service that an organization requires. This is where a facility management gap analysis comes into play. In this comprehensive guide, we will explore what a facility management gap analysis is, why it’s essential, and how to conduct one effectively.
What is a Facility Management Gap Analysis?
A facility management gap analysis is a systematic process used to identify and bridge the gap between the current state of facility operations and the desired state. It helps organizations understand where they are lacking in terms of resources, processes, and outcomes. This analysis can cover various aspects such as maintenance, energy efficiency, safety protocols, and overall facility performance.
The ultimate goal of a gap analysis is to develop an action plan that addresses the identified gaps, ensuring that the facility operates at an optimal level. This process not only improves the facility’s functionality but also enhances the overall efficiency and effectiveness of the organization.
Why Conduct a Facility Management Gap Analysis?
Conducting a facility management gap analysis is essential for several reasons:
- Identify Weaknesses: It helps pinpoint areas where the current facility management practices are falling short. This could be due to outdated processes, insufficient resources, or lack of trained personnel.
- Improve Efficiency: By identifying gaps, organizations can streamline their operations, reduce waste, and optimize resource utilization, leading to cost savings and increased productivity.
- Enhance Safety and Compliance: Ensuring that the facility meets all safety and regulatory requirements is critical. A gap analysis can highlight areas of non-compliance, helping the organization to address these issues before they lead to more significant problems.
- Plan for the Future: A gap analysis provides a clear understanding of where the facility currently stands and what needs to be done to reach the desired state. This information is invaluable for strategic planning and budgeting.
- Support Decision-Making: The insights gained from a gap analysis can inform decision-making at all levels, ensuring that resources are allocated effectively and that improvements are prioritized based on their impact.
Steps to Conduct a Facility Management Gap Analysis
Now that we understand the importance of a facility management gap analysis, let’s delve into the steps involved in conducting one.
Step 1: Define the Scope of the Analysis
The first step in conducting a facility management gap analysis is to define the scope. This involves determining what aspects of facility management will be analyzed and to what extent. The scope may include areas such as:
- Maintenance Management: Assessing the effectiveness of maintenance schedules, the condition of equipment, and the response time for repairs.
- Energy Management: Evaluating energy consumption, identifying opportunities for energy savings, and assessing the efficiency of energy management systems.
- Safety and Compliance: Reviewing safety protocols, compliance with local regulations, and the effectiveness of safety training programs.
- Space Utilization: Analyzing how space is used within the facility, identifying underutilized areas, and exploring opportunities for better space management.
- Environmental Impact: Assessing the facility’s environmental footprint, including waste management, water usage, and sustainability initiatives.
Clearly defining the scope will help ensure that the analysis is focused and that the findings are actionable.
Step 2: Gather Data and Information
Once the scope is defined, the next step is to gather data and information related to the areas being analyzed. This data collection process can be extensive, depending on the scope of the analysis, and may include:
- Facility Audits: Conducting physical inspections of the facility to assess the condition of equipment, infrastructure, and systems.
- Surveys and Interviews: Gathering input from facility management staff, employees, and other stakeholders to understand their perspectives on the current state of the facility.
- Review of Documentation: Analyzing maintenance records, energy bills, safety reports, and other relevant documents to gain insights into the facility’s operations.
- Benchmarking: Comparing the facility’s performance against industry standards or similar facilities to identify areas where it falls short.
Accurate and comprehensive data collection is critical to the success of the gap analysis, as it provides the foundation for identifying gaps and developing improvement strategies.
Step 3: Analyze the Current State
With the data in hand, the next step is to analyze the current state of facility management. This involves evaluating the information collected to identify strengths, weaknesses, opportunities, and threats (SWOT analysis) related to the facility’s operations.
During this analysis, consider the following questions:
- Are maintenance schedules being followed, and are they effective in preventing breakdowns?
- Is energy consumption in line with industry benchmarks, or are there opportunities for improvement?
- Are safety protocols up to date, and is the facility compliant with all relevant regulations?
- Is the available space being utilized efficiently, or is there potential for better space management?
- What environmental impact does the facility have, and how can it be minimized?
The answers to these questions will help you identify gaps between the current state and the desired state of facility management.
Step 4: Define the Desired State
After analyzing the current state, it’s essential to define the desired state of facility management. This involves setting clear, measurable goals for each area of focus. For example:
- Maintenance Management: The desired state may involve reducing the frequency of equipment breakdowns by 20% and improving response times for repairs to less than 24 hours.
- Energy Management: The goal could be to reduce energy consumption by 15% over the next two years through the implementation of energy-efficient systems and practices.
- Safety and Compliance: The desired state might include achieving full compliance with all safety regulations and reducing the number of workplace accidents by 30%.
- Space Utilization: The objective could be to increase space utilization by 25% through better planning and management of available space.
- Environmental Impact: The desired state may involve reducing the facility’s carbon footprint by 10% and increasing recycling rates by 50%.
Defining the desired state provides a clear target for the facility management team to work towards and sets the stage for developing an action plan.
Step 5: Identify the Gaps
With both the current state and desired state defined, the next step is to identify the gaps between them. This involves comparing the current state of facility management with the desired state to pinpoint areas where improvements are needed.
For each gap identified, consider the following:
- Magnitude: How significant is the gap? Is it a minor issue that can be addressed with minimal effort, or is it a major challenge that requires substantial resources to overcome?
- Impact: What is the potential impact of closing the gap? Will it lead to cost savings, improved safety, better space utilization, or enhanced environmental performance?
- Priority: How urgent is the need to address the gap? Are there any immediate risks or opportunities that should be prioritized?
Identifying and prioritizing gaps will help you focus your efforts on the areas that will have the most significant impact on the facility’s performance.
Step 6: Develop an Action Plan
Once the gaps have been identified and prioritized, the next step is to develop an action plan to address them. This plan should outline the specific steps that need to be taken to close each gap, along with timelines, responsibilities, and resource requirements.
Key elements of an action plan include:
- Objectives: Clearly define the objectives for each gap identified. What do you aim to achieve by addressing this gap?
- Actions: Outline the specific actions that need to be taken to close the gap. This could involve implementing new processes, upgrading equipment, providing additional training, or making changes to existing practices.
- Responsibilities: Assign responsibilities to specific individuals or teams for each action item. Who will be responsible for implementing the changes, and who will oversee the process?
- Timelines: Establish timelines for completing each action item. When should each task be completed, and what are the key milestones along the way?
- Resources: Identify the resources needed to implement the action plan. This could include budget, personnel, equipment, or external support.
A well-developed action plan is critical to the success of the facility management gap analysis, as it provides a clear roadmap for closing the identified gaps and achieving the desired state.
Step 7: Monitor Progress and Adjust as Needed
The final step in the facility management gap analysis process is to monitor progress and make adjustments as needed. This involves regularly reviewing the implementation of the action plan, tracking progress against the established timelines and objectives, and making any necessary adjustments to ensure success.
Consider the following when monitoring progress:
- Key Performance Indicators (KPIs): Establish KPIs to measure the success of the action plan. These could include metrics such as equipment downtime, energy consumption, safety incidents, or space utilization rates.
- Regular Reviews: Schedule regular reviews of the action plan to assess progress and identify any challenges or obstacles that may have arisen.
- Continuous Improvement: Use the insights gained from the monitoring process to continuously improve facility management practices. This may involve updating the action plan, revising goals, or implementing new strategies.
Monitoring progress is essential to ensure that the gaps identified in the analysis are effectively addressed and that the facility management team remains on track to achieve the desired state.
Conclusion
A facility management gap analysis is a powerful tool that enables organizations to identify areas of improvement, optimize operations, and achieve their facility management goals. By following the steps outlined in this guide, you can conduct a thorough gap analysis that provides valuable insights into your facility’s current state and helps you develop a clear, actionable plan for closing the gaps.
Whether your focus is on maintenance management, energy efficiency, safety and compliance, space utilization, or environmental impact, a gap analysis can provide the information and direction needed.