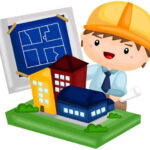
How to Develop a Facility Management Dashboard
August 26, 2024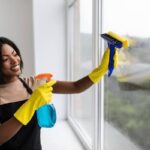
Best Practices for Cleaning and Sanitation
September 4, 2024Preventive maintenance (PM) is a strategic approach to ensuring the longevity and functionality of your facility. Unlike reactive maintenance, where issues are fixed after they arise, preventive maintenance focuses on regular upkeep to prevent potential problems before they occur. Developing a preventive facility maintenance program may seem daunting, but with the right framework, it becomes a practical and highly beneficial task. This article outlines a step-by-step guide to building an effective preventive maintenance program for your facility.
What is Preventive Maintenance?
Preventive maintenance is the process of routinely inspecting, servicing, and repairing equipment, systems, and infrastructure to ensure they remain in good working order. Its goal is to reduce downtime, extend the life of assets, and save money by preventing unexpected breakdowns. Regularly maintaining equipment can help avoid costly repairs, increase safety, and optimize the performance of your facility.
Why is Preventive Maintenance Important?
- Cost savings: Unscheduled repairs and replacements can be expensive. Preventive maintenance helps catch minor issues before they escalate into larger, more costly problems.
- Improved efficiency: Well-maintained systems operate at peak efficiency, which can reduce energy consumption and increase the overall productivity of your facility.
- Safety and compliance: Regular maintenance ensures that all safety systems, such as fire alarms and emergency exits, are functioning properly, thus meeting compliance standards.
- Asset longevity: Routine maintenance extends the life of equipment, reducing the need for premature replacements.
Steps to Develop a Preventive Maintenance Program
Creating a preventive maintenance program requires thoughtful planning and consistent execution. Here are the key steps to follow.
1. Assess Your Current Maintenance Practices
Before creating a new program, it’s important to evaluate your existing maintenance processes. This assessment helps you identify gaps, inefficiencies, and equipment that may need more attention. Consider the following questions:
- How is maintenance currently handled?
- Are repairs done reactively, or is there a schedule in place?
- How much downtime is caused by equipment failures?
- What is the cost of emergency repairs?
This assessment will provide insight into what’s working and what needs improvement, giving you a clear starting point for your preventive maintenance program.
2. Identify Critical Assets and Equipment
Once you have assessed your current maintenance practices, the next step is to identify the critical assets and equipment within your facility. These are the machines, systems, or infrastructure elements that are most essential to your operation and would cause significant disruption or financial loss if they fail.
- Machinery and Equipment: Focus on high-cost or mission-critical machines.
- Safety Systems: Ensure that all safety equipment (fire alarms, extinguishers, emergency lights, etc.) is included in the plan.
- HVAC Systems: Heating, ventilation, and air conditioning systems are vital for maintaining a comfortable and safe work environment.
- Electrical and Plumbing: These systems are often out of sight but critical to daily operations.
3. Create an Asset Inventory
An asset inventory is a comprehensive list of all the equipment, systems, and infrastructure within your facility that require maintenance. For each item, include details such as:
- Manufacturer information
- Model and serial numbers
- Date of purchase or installation
- Maintenance history
- Warranty information
- Service contracts (if applicable)
This inventory provides a foundation for your preventive maintenance program, helping to ensure that nothing is overlooked.
4. Determine Maintenance Tasks and Schedules
The next step is to establish a maintenance schedule for each piece of equipment based on manufacturer recommendations, past performance, and the operating environment. The frequency of maintenance will vary depending on the equipment and its usage. For example:
- Daily/Weekly Tasks: Simple inspections such as checking for leaks, unusual noises, or vibrations.
- Monthly/Quarterly Tasks: Cleaning filters, lubricating moving parts, or calibrating equipment.
- Annual/Biannual Tasks: More thorough inspections and testing of safety systems, HVAC cleaning, or electrical system checks.
It’s important to document each task in detail, so the maintenance team knows exactly what is required. This includes specifying the tools and parts needed, the estimated time to complete the task, and the person responsible for the job.
5. Assign Responsibilities
A successful preventive maintenance program depends on clear lines of responsibility. Assign specific tasks to individuals or teams, ensuring they are aware of their roles and the importance of regular maintenance. This can be done by:
- Designating a Maintenance Manager: This person will oversee the entire preventive maintenance program, ensure adherence to schedules, and manage the maintenance team.
- Technicians and Engineers: Depending on the complexity of the equipment, some tasks may require specialized skills. Make sure qualified personnel handle these tasks.
- External Contractors: For certain equipment, such as elevators or HVAC systems, you may need to hire external contractors to handle maintenance. Ensure they are aware of your program and schedules.
6. Implement a Maintenance Management System (CMMS)
To keep track of all the scheduled maintenance tasks, it’s advisable to use a computerized maintenance management system (CMMS). A CMMS helps organize and automate maintenance processes, making it easier to track the performance of your preventive maintenance program.
- Work Order Management: The system generates work orders for scheduled tasks, ensuring nothing is overlooked.
- Asset Tracking: CMMS stores all asset information, including maintenance history and upcoming tasks.
- Report Generation: The system can generate reports on maintenance costs, performance, and trends.
- Alerts and Notifications: CMMS sends reminders when tasks are due, ensuring that maintenance schedules are followed.
With a CMMS in place, managing preventive maintenance becomes much more efficient and streamlined.
7. Develop a Documentation Process
Thorough documentation is key to a successful preventive maintenance program. Keeping accurate records of each task performed ensures that your program is transparent and helps identify trends or recurring issues.
For each maintenance task, make sure to document:
- The date and time the task was completed
- Who performed the task
- The specific work done
- Any issues or repairs required
- The current condition of the equipment
This documentation helps improve the accuracy of your maintenance schedules and provides valuable data for future decisions about asset replacement or upgrades.
8. Train Your Maintenance Team
To effectively implement your preventive maintenance program, your team must be properly trained. Ensure that your technicians understand the specific maintenance tasks they are responsible for and are trained in the proper procedures and safety protocols.
- Provide Equipment-Specific Training: Technicians should be familiar with the operation, maintenance, and repair of the equipment they will be servicing.
- Safety Training: Emphasize safety practices, including the use of personal protective equipment (PPE), lockout/tagout procedures, and how to safely handle hazardous materials.
- CMMS Training: If you are using a CMMS, ensure that your team is trained on how to use the system effectively for scheduling and documentation.
By investing in proper training, you increase the likelihood of a successful preventive maintenance program.
9. Monitor and Adjust the Program
Once your preventive maintenance program is up and running, it’s important to monitor its performance and make adjustments as needed. Regularly review maintenance data and reports to identify areas for improvement. Key metrics to track include:
- Mean Time Between Failures (MTBF): This measures the average time between equipment breakdowns. A high MTBF indicates that your preventive maintenance program is effective.
- Mean Time to Repair (MTTR): This measures how quickly repairs are completed when equipment does fail. A lower MTTR means your team is resolving issues efficiently.
- Equipment Downtime: Track the amount of time equipment is out of service. Preventive maintenance should minimize unplanned downtime.
- Maintenance Costs: Monitor the overall cost of your preventive maintenance program, including labor, parts, and external contractors.
Regularly reviewing these metrics will help you fine-tune your preventive maintenance program and ensure that it continues to provide value to your facility.
10. Involve All Stakeholders
Preventive maintenance is not the responsibility of the maintenance team alone. It requires the involvement of multiple departments and stakeholders, including:
- Management: Ensure that upper management is supportive of the preventive maintenance program and understands the long-term cost savings and benefits.
- Operations Staff: Train operators on basic maintenance tasks such as cleaning and inspecting equipment between scheduled maintenance visits.
- Procurement Team: Work with procurement to ensure that spare parts and materials are available when needed for preventive maintenance tasks.
Collaboration across departments will ensure the smooth implementation of your preventive maintenance program.
Common Challenges in Implementing Preventive Maintenance
While preventive maintenance offers many benefits, it’s not without its challenges. Some common obstacles include:
1. Lack of Time and Resources
Facilities that are already struggling to keep up with reactive maintenance may find it difficult to allocate time and resources to preventive tasks. However, it’s important to emphasize that preventive maintenance will save time and money in the long run by reducing the need for emergency repairs.
2. Resistance to Change
Some employees may resist the implementation of a preventive maintenance program, especially if they are accustomed to a reactive approach. Clear communication about the benefits of preventive maintenance, along with proper training, can help overcome this resistance.
3. Inconsistent Execution
A preventive maintenance program is only effective if it is consistently followed. This is where a CMMS can help, by automating scheduling and sending reminders to ensure that tasks are completed on time.
4. Budget Constraints
While preventive maintenance can lead to long-term savings, there may be initial costs associated with setting up the program, such as purchasing a CMMS or training staff. It’s important to secure buy-in from management by demonstrating the potential cost savings of preventive maintenance.
Conclusion
Developing a preventive facility maintenance program is an investment in the long-term health and efficiency of your facility. By taking a proactive approach to maintenance, you can reduce downtime, extend the lifespan of your equipment, and save money on emergency repairs.