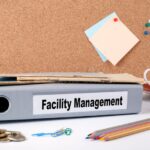
Facility Management Challenges and How to Overcome Them
September 18, 2024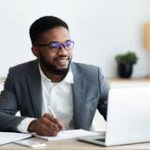
How to Conduct a Space Utilization Study
September 25, 2024A Facility Condition Assessment (FCA) is an essential process for maintaining and improving the performance and value of buildings and other infrastructure. It helps facility managers and owners assess the physical state of their assets and plan for future repairs, replacements, and renovations. This article provides a comprehensive guide on how to conduct a Facility Condition Assessment, including the steps involved, tools required, and best practices.
What is a Facility Condition Assessment?
A Facility Condition Assessment is a thorough evaluation of the physical condition of a building or facility. It is a systematic process designed to identify the condition of various building components, such as the structure, mechanical systems, electrical systems, plumbing, and finishes. The goal of an FCA is to provide a detailed report on the state of the facility and estimate the cost of repairs or upgrades needed to maintain its performance and safety.
FCAs are often conducted for various purposes, including:
- Asset Management: To prioritize repairs and upgrades for large portfolios of buildings.
- Capital Planning: To inform long-term financial planning for maintenance and renovations.
- Risk Management: To identify potential safety hazards and compliance issues.
- Sustainability Goals: To assess energy efficiency and environmental performance.
When Should a Facility Condition Assessment Be Conducted?
An FCA is typically conducted at different stages of a facility’s lifecycle, including:
- Pre-purchase: Before acquiring a facility, an FCA helps identify any potential issues and associated costs.
- Regular Maintenance: Facility managers may schedule routine assessments every 3-5 years to maintain asset performance.
- Before Major Renovations: An FCA helps evaluate the condition of existing systems and materials before planning major renovations or upgrades.
The frequency of an FCA will depend on the age, complexity, and usage of the facility, as well as regulatory or organizational requirements.
Steps to Conduct a Facility Condition Assessment
Conducting a Facility Condition Assessment requires a systematic approach to gather data, analyze the findings, and present the results in a useful format. Below are the key steps involved in the process:
1. Pre-Assessment Planning
Before beginning the actual assessment, thorough planning is essential. This involves:
- Defining the Scope: Determine the scope of the assessment, including which parts of the facility will be evaluated, such as structural components, HVAC systems, electrical systems, and interior finishes. Identify whether the assessment is for a single building or an entire portfolio.
- Assembling a Team: The assessment team should consist of qualified professionals with expertise in architecture, engineering, facility management, or construction. The team may include mechanical and electrical engineers, architects, and building inspectors.
- Gathering Documentation: Collect relevant documentation such as as-built drawings, maintenance logs, past repair records, warranties, and equipment manuals. This will provide valuable background information for the assessment.
- Setting a Timeline and Budget: Determine the timeline for the assessment and establish a budget for hiring professionals, acquiring tools, and processing data.
2. On-Site Inspection
The on-site inspection is the core of the Facility Condition Assessment. It involves a detailed examination of all critical components and systems of the facility. Here are the primary steps involved in the inspection process:
A. Exterior Inspection
The exterior of a facility can reveal important clues about its overall condition. The inspection typically covers:
- Structural Integrity: Evaluate the building’s foundation, walls, roof, and load-bearing components for signs of damage, cracking, or shifting.
- Exterior Finishes: Assess the condition of exterior surfaces, such as brick, siding, windows, and doors. Look for signs of wear, moisture penetration, or deterioration.
- Site Conditions: Check the condition of the surrounding site, including sidewalks, parking lots, drainage systems, landscaping, and exterior lighting.
B. Interior Inspection
During the interior inspection, assess the condition of various components that impact the safety, comfort, and functionality of the building:
- HVAC Systems: Examine the heating, ventilation, and air conditioning systems for operational efficiency, leaks, or other issues.
- Electrical Systems: Inspect wiring, lighting, and electrical panels. Check for code compliance, fire hazards, or outdated components.
- Plumbing Systems: Check water supply lines, drainage systems, fixtures, and water heaters for leaks or corrosion.
- Finishes and Fixtures: Evaluate interior finishes such as flooring, walls, ceilings, and cabinetry for signs of wear and tear.
C. Mechanical and Structural Systems
Assessing the mechanical and structural systems is crucial for evaluating the long-term performance of the building. This includes:
- Mechanical Equipment: Examine equipment such as boilers, chillers, generators, and elevators. Look for signs of excessive wear, operational inefficiency, or safety concerns.
- Structural Components: Inspect beams, columns, and load-bearing walls for cracks, signs of settling, or water damage.
3. Data Collection and Documentation
During the inspection, it’s important to document findings thoroughly. This includes taking detailed notes, photographs, and videos. Each component or system should be recorded, and any deficiencies or concerns should be noted for further analysis. Using a checklist or facility assessment software can help ensure that no key elements are overlooked.
Make sure to collect the following data:
- Condition Ratings: Assign a condition rating to each component (e.g., good, fair, poor) to represent its current state.
- Remaining Useful Life: Estimate the remaining useful life of building systems and components based on age and current condition.
- Cost Estimates: Document the estimated cost for repairing, replacing, or upgrading systems that are in poor condition.
- Compliance Issues: Identify any code violations or safety hazards that need immediate attention.
4. Analysis and Reporting
Once the data is collected, it’s time to analyze the findings and prepare a comprehensive report. This report will serve as a roadmap for future maintenance and capital planning. The analysis typically includes:
- Condition Index: The Facility Condition Index (FCI) is a key metric used to assess the condition of a facility. It is calculated by dividing the cost of necessary repairs by the replacement value of the facility. A higher FCI indicates a facility in poor condition.
- Deficiency Prioritization: Prioritize the identified deficiencies based on severity, safety concerns, and financial impact. Immediate safety concerns should take precedence over cosmetic issues.
- Capital Planning: The report should provide recommendations for future capital investments, including suggested timelines for repairs and upgrades. This helps stakeholders plan for long-term budgeting and resource allocation.
5. Maintenance and Follow-Up
After the Facility Condition Assessment is completed, facility managers should use the findings to develop a proactive maintenance plan. This involves:
- Preventive Maintenance: Implementing a schedule for regular inspections, repairs, and system upgrades to prevent costly failures or downtime.
- Monitoring Systems: Continuously monitoring the performance of key building systems to ensure they remain in good condition and operate efficiently.
- Record Keeping: Maintain an updated record of all repairs, replacements, and maintenance activities for future reference and assessments.
6. Using Technology in Facility Condition Assessments
Technology plays an increasingly important role in the Facility Condition Assessment process. Several tools and software platforms can streamline data collection, analysis, and reporting. Some examples include:
- Drones and Aerial Imaging: Drones equipped with cameras can provide detailed aerial views of a facility’s roof, exterior, and surrounding site, making it easier to detect issues such as cracks or water damage.
- 3D Scanning and BIM (Building Information Modeling): 3D scanners and BIM software allow for highly detailed digital models of the facility. This can be useful for tracking changes in the building’s condition over time and improving accuracy in cost estimates.
- Facility Management Software: Dedicated software platforms help organize data, manage work orders, and track maintenance tasks. These tools allow facility managers to monitor the condition of assets in real time.
7. Best Practices for Conducting an FCA
To ensure a successful Facility Condition Assessment, consider the following best practices:
- Engage Qualified Professionals: Always work with certified inspectors, engineers, and facility management professionals who have experience conducting FCAs. Their expertise ensures accurate assessments and actionable recommendations.
- Prioritize Safety: Address any safety hazards immediately, especially those related to electrical systems, structural integrity, or fire code violations.
- Document Everything: Detailed documentation, including photographs, videos, and condition ratings, is crucial for creating an accurate record of the facility’s condition.
- Be Proactive: Don’t wait for major issues to arise. Regularly scheduled assessments and preventive maintenance can extend the life of the facility and reduce long-term costs.
Conclusion
Conducting a Facility Condition Assessment is a valuable process for ensuring the long-term health and safety of a facility. By following a systematic approach—from pre-assessment planning to analysis and reporting—facility managers can make informed decisions about maintenance, repairs, and capital investments. Regular assessments, combined with modern technology and proactive maintenance, will help extend the life of building systems, improve performance, and reduce operating costs.