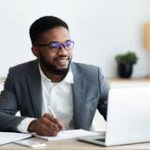
How to Conduct a Space Utilization Study
September 25, 2024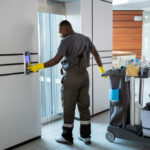
The Ultimate Guide to Choosing a Facility Management Cleaning Service
September 30, 2024Ensuring the safety of everyone within a facility is crucial for the wellbeing of employees and the overall success of the business. A well-developed health and safety program is a proactive way to identify, address, and prevent risks before accidents occur. This article will guide you through the steps to implement an effective health and safety program in your facility, regardless of its size or industry.
1. Understand the Importance of a Health and Safety Program
A health and safety program is designed to prevent workplace injuries, illnesses, and accidents. It serves not only as a legal requirement in many regions but also as a moral responsibility. Beyond meeting regulations, a well-executed program improves employee morale, reduces absenteeism, and enhances productivity. Safe working environments tend to attract and retain talent, creating a positive workplace culture.
Benefits of a Health and Safety Program
- Reduced Accidents: A structured approach to safety can prevent accidents from happening.
- Cost Savings: By avoiding workplace injuries, you save on medical costs, legal fees, and compensation.
- Legal Compliance: A solid health and safety plan helps you comply with governmental safety regulations, reducing the risk of fines or sanctions.
- Increased Employee Engagement: Employees feel valued when their wellbeing is prioritized.
2. Assess Current Safety Conditions
Before developing a health and safety program, it’s essential to assess the current safety conditions of your facility. Conduct a thorough safety audit that evaluates risks, potential hazards, and compliance with local and federal regulations.
Conducting a Safety Audit
A safety audit should include:
- Workplace Inspections: Examine all areas of the facility for potential risks, such as improperly stored materials, malfunctioning equipment, or poor lighting.
- Employee Feedback: Engage with employees to identify overlooked hazards or areas of concern.
- Accident Records: Review past accident reports to identify patterns or recurring issues that need attention.
- Compliance Check: Ensure that the facility meets all local, state, and federal regulations for workplace safety.
After gathering this information, prioritize the most urgent safety issues and develop a plan to address them.
3. Set Clear Safety Goals and Objectives
Once the current safety conditions are understood, it’s time to establish clear goals and objectives. These should be specific, measurable, and achievable, taking into account the facility’s size, industry, and unique risks. Your goals may include reducing the number of accidents, improving safety training, or updating safety equipment.
Examples of Safety Goals:
- Reduce workplace injuries by 20% in the next year.
- Provide safety training for 100% of employees within six months.
- Conduct monthly safety drills to improve emergency response times.
Having well-defined goals provides the team with a clear direction and helps track progress over time.
4. Develop a Written Safety Policy
A written safety policy is the foundation of your health and safety program. This document should outline the facility’s commitment to safety and define the roles and responsibilities of management and employees. It serves as a roadmap for implementing safety measures and is often required by law.
Key Elements of a Safety Policy:
- Management Commitment: A statement from senior management affirming their commitment to safety.
- Employee Involvement: Clearly outline how employees are expected to participate in the safety program.
- Hazard Identification: Include a process for identifying hazards and how they will be addressed.
- Emergency Procedures: Provide detailed instructions on how to respond to emergencies, including evacuation routes and contact information for emergency services.
The safety policy should be communicated to all employees and updated regularly to reflect any changes in the workplace or regulations.
5. Create a Safety Committee
A safety committee is an effective way to involve employees in the health and safety program. This team should consist of representatives from different departments who collaborate to identify hazards, recommend solutions, and review safety procedures.
Roles of a Safety Committee:
- Regular Inspections: Conduct regular safety inspections to identify hazards and ensure compliance.
- Accident Investigations: Review accident reports and investigate root causes.
- Safety Training: Organize and conduct safety training sessions.
- Policy Updates: Recommend updates to the safety policy based on findings from inspections and investigations.
The committee should meet regularly and report back to management on safety-related issues.
6. Provide Employee Training
Training is a critical component of any health and safety program. Employees must be equipped with the knowledge and skills to recognize hazards, follow safety protocols, and respond effectively to emergencies.
Types of Safety Training:
- New Employee Orientation: Provide safety training to new employees as part of their onboarding process.
- Ongoing Training: Regularly update employees on new safety protocols, equipment, or changes in the workplace.
- Emergency Response Training: Teach employees how to respond to emergencies such as fires, chemical spills, or medical incidents.
- Job-Specific Training: Tailor training sessions to the specific roles and tasks of employees, ensuring they understand the unique risks they may encounter.
Training should be practical and interactive, using hands-on exercises and real-life scenarios to reinforce learning.
7. Implement Hazard Identification and Control Measures
Hazard identification and control are central to maintaining a safe workplace. Establish procedures for recognizing hazards and implementing control measures to reduce the risk of injury.
Steps for Hazard Control:
- Identify Hazards: Conduct regular inspections to spot potential risks in equipment, machinery, or processes.
- Assess Risk: Determine the likelihood and severity of accidents occurring as a result of these hazards.
- Control Measures: Implement control measures using a hierarchy of controls:
- Elimination: Remove the hazard from the workplace.
- Substitution: Replace hazardous materials or equipment with safer alternatives.
- Engineering Controls: Use physical changes, such as ventilation systems or safety guards, to reduce risks.
- Administrative Controls: Implement policies or procedures, such as rotating shifts to reduce exposure to hazards.
- Personal Protective Equipment (PPE): Provide PPE such as gloves, helmets, or safety goggles to protect employees.
Hazards should be continuously monitored, and control measures should be adjusted as needed.
8. Ensure Proper Incident Reporting and Investigation
Despite best efforts, incidents may still occur. Establishing a formal process for incident reporting and investigation ensures that accidents are properly documented and addressed to prevent future occurrences.
Steps for Incident Reporting:
- Immediate Reporting: Encourage employees to report any accidents or near-misses immediately.
- Investigation: Conduct thorough investigations to determine the root cause of the incident.
- Corrective Actions: Based on the findings, implement corrective actions to prevent similar incidents.
- Documentation: Maintain detailed records of all incidents, investigations, and corrective actions for future reference.
Investigating near-misses is especially important, as these events often signal potential hazards that could result in serious accidents if left unaddressed.
9. Implement Emergency Preparedness and Response Plans
Emergencies can happen at any time, and preparedness is essential to minimizing harm. A well-developed emergency response plan ensures that employees know how to respond quickly and effectively in the event of an emergency.
Elements of an Emergency Response Plan:
- Evacuation Procedures: Clearly marked evacuation routes and assembly points should be in place.
- Emergency Contacts: Post emergency phone numbers and contacts in visible locations throughout the facility.
- First Aid: Train employees in basic first aid and ensure that first aid kits are easily accessible.
- Fire Safety: Install fire alarms, extinguishers, and sprinkler systems, and conduct regular fire drills.
Review and update the emergency response plan regularly, ensuring all employees are familiar with the procedures.
10. Monitor and Evaluate the Program’s Effectiveness
A health and safety program is not a one-time effort. Continuous monitoring and evaluation are crucial to ensuring the program remains effective and relevant to the facility’s evolving needs.
Key Performance Indicators (KPIs) to Monitor:
- Number of Accidents: Track the number and severity of accidents over time.
- Employee Feedback: Regularly survey employees to gather feedback on safety concerns and suggestions for improvement.
- Training Completion Rates: Monitor the percentage of employees who have completed safety training.
- Inspection Results: Review the results of safety inspections and audits.
Use this data to assess the effectiveness of the program and make any necessary adjustments.
11. Foster a Safety Culture
Creating a safety culture within the facility is perhaps the most important aspect of a successful health and safety program. When safety becomes a core value that is embraced by all employees, it leads to a safer and more productive work environment.
How to Foster a Safety Culture:
- Lead by Example: Management should model safe behavior and prioritize safety in all decisions.
- Encourage Open Communication: Create an environment where employees feel comfortable reporting hazards or suggesting improvements without fear of reprisal.
- Reward Safe Behavior: Recognize and reward employees who demonstrate a commitment to safety.
- Continuous Improvement: Promote the idea that safety is an ongoing effort, and encourage employees to always look for ways to improve.
Conclusion
Implementing a health and safety program in facilities is a comprehensive process that requires careful planning, consistent execution, and continuous improvement. By assessing risks, setting clear goals, training employees, and fostering a culture of safety, you can create a workplace environment that protects employees, enhances productivity, and ensures compliance with regulations. Prioritizing safety is not only a legal obligation—it is a moral responsibility that benefits everyone involved.